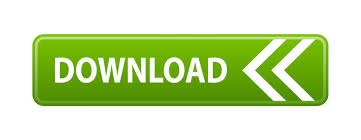
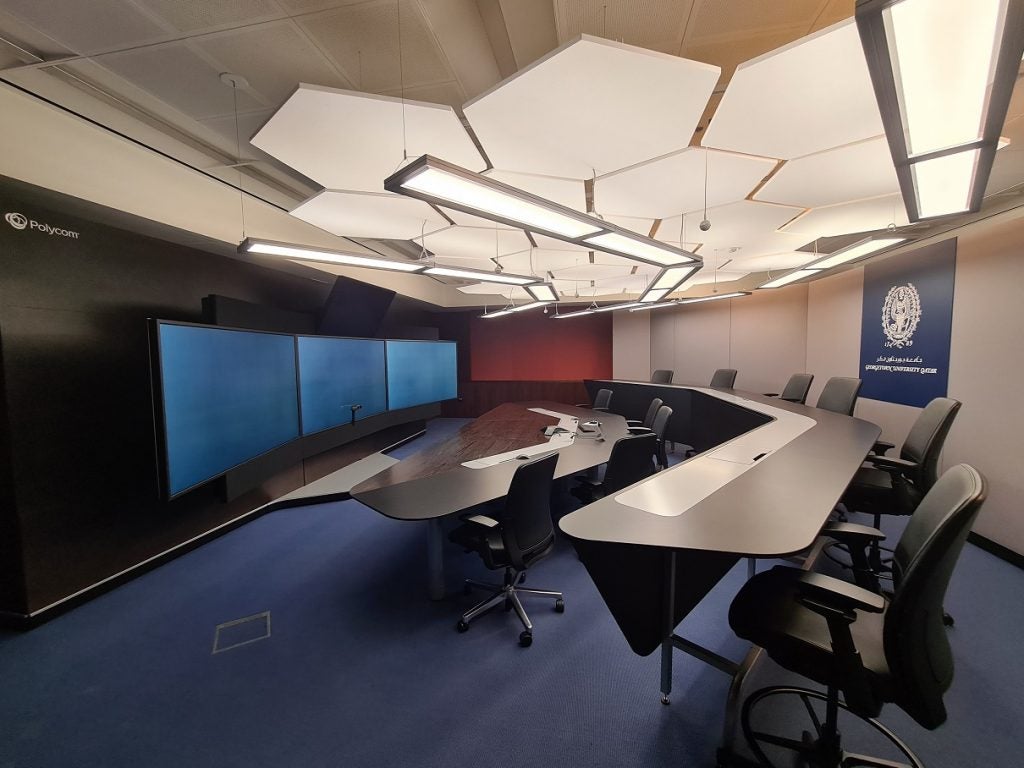
In 1969, Bayer exhibited an all-plastic car in Düsseldorf, Germany. During the 1960s, automotive interior safety components, such as instrument and door panels, were produced by back-filling thermoplastic skins with semi-rigid foam. In 1967, urethane-modified polyisocyanurate rigid foams were introduced, offering even better thermal stability and flammability resistance. The availability of chlorofluoroalkane blowing agents, inexpensive polyether polyols, and methylene diphenyl diisocyanate (MDI) allowed polyurethane rigid foams to be used as high-performance insulation materials. In 1960 more than 45,000 metric tons of flexible polyurethane foams were produced. Monsanto/ Bayer joint venture, also began making polyurethane chemicals. Polyether polyols were cheaper, easier to handle and more water-resistant than polyester polyols, and became more popular. In 1956 DuPont introduced polyether polyols, specifically poly(tetramethylene ether) glycol, and BASF and Dow Chemical started selling polyalkylene glycols in 1957. Linear fibers were produced from hexamethylene diisocyanate (HDI) and 1,4-Butanediol (BDO). These materials were also used to produce rigid foams, gum rubber, and elastomers. Polyisocyanates became commercially available in 1952, and production of flexible polyurethane foam began in 1954 by combining toluene diisocyanate (TDI) and polyester polyols. Early work focused on the production of fibres and flexible foams and PUs were applied on a limited scale as aircraft coating during World War II. The new polymers had some advantages over existing plastics that were made by polymerizing olefins or by polycondensation, and were not covered by patents obtained by Wallace Carothers on polyesters. Otto Bayer and his coworkers at IG Farben in Leverkusen, Germany, first made polyurethanes in 1937. Otto Bayer in 1952 demonstrating his creation This is a sufficiently high volume for it to be regarded as a commodity plastic. Global production in 2019 was some 25 million metric tonnes, accounting for about 6% of all polymers produced in that year. Both the isocyanates and polyols used to make polyurethanes contain, on average, two or more functional groups per molecule. Since polyurethanes contain two types of monomers, which polymerise one after the other, they are classed as alternating copolymers.
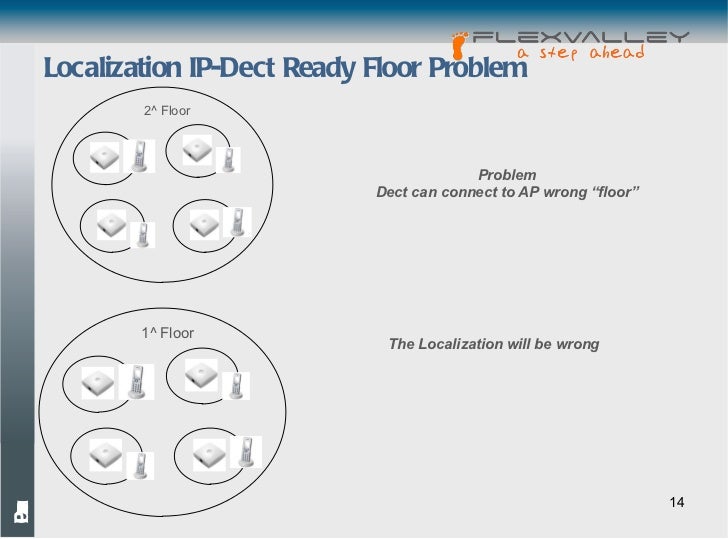
Polyurethane polymers are traditionally and most commonly formed by reacting a di- or triisocyanate with a polyol. Of these, foams are the largest single application, accounting for 67% of all polyurethane produced in 2016.

This chemical variety allows for polyurethanes with very different physical properties, leading to an equally wide range of different applications including: rigid and flexible foams, varnishes and coatings, adhesives, electrical potting compounds, and fibres such as spandex and PUL. In contrast to other common polymers such as polyethylene and polystyrene, polyurethane is produced from a wide range of starting materials ( monomers) and is therefore a class of polymers, rather than a distinct compound. Polyurethane (often abbreviated PUR and PU) is a commonly encountered polymer composed of organic units joined by carbamate (urethane) links.
#Polycom flex full size
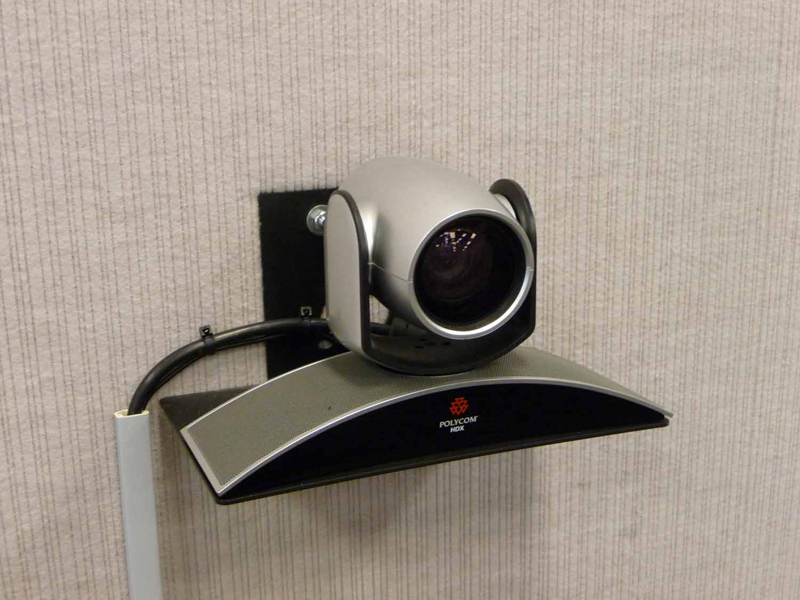
#Polycom flex plus
Integrated with Polycom 3D Voice, digital ceiling microphones and a system that allows for annotation and whiteboarding from your own laptop or mobile device, the RealPresence Immersive Studio Flex even includes Skype for Business integration plus Polycom RealConnect. Everything is 4K (even the low-res sources are upscaled to 4K) and the system uses multiple 65” displays to immerse attendees. The new Polycom RealPresence Immersive Studio Flex is their latest immersive room videoconferencing system.
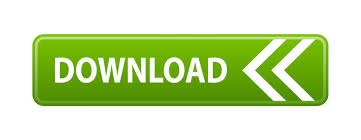